
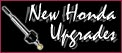
|
At
left are two compressor sections each of the five stage Rx8
configuration. One assembled the other stacked separately. Look
closely to see the zero tip clearance stators. All these
components are machined from solid bar stock of various alloys.
HISTORY
The first use of axial flow compressors for automotive
supercharging was by Norman Latham Of West Palm Beach Florida in
1956. This unit was known as the Latham Supercharger and was
sold until 1965. These were built with a sheet-metal blade
installed into a ring and locked by another ring. Very clever
way of getting a wing into a disk. Trouble was there was no
aerodynamic shape and the time to build was totally
unacceptable.
These were made for almost all cars being produced at that time.
They were supplied with Carter one barrel side draft
carburetors. In two and four carb set ups.
There were over 600 produced. Most are still in running
condition and sell at a premium on the vintage car market.
The Latham company was sold to Richard Paul in 1982. At that
time the old design was abandoned for a more modern design that
included true aerodynamic shapes to the blades. A new method of
construction was also devised. The use of lost wax casting was
utilized. In general appearance the two superchargers might look
the same to an untrained eye. However looking closer there are
major differences in the two. Aerodynamically shaped volutes are
used on the new design. Carburetion is done in modern style with
Weber side draft carbs as well as Four barrel types. Electronic
fuel injection was utilized in the last of these to be produced
in the early '90's.
Production of the cast units stopped in 1990. A new method of
producing blowers was devised building the whole unit from
billet bar stock. This was very superior to any other method so
far. This allowed for any size or shape of wing to be utilized.
Thus a true turbine like shrinking area compressor was available
at a reasonable price. Trouble was that price was not reasonable
in aftermarket automotive terms.
While several of these were made in different sizes for specific
applications there was not enough of a market at that cost.
Another size was experimented with at that time. Since the new
method allowed for increases performance a smaller package was
designed. Three of this type were produced in prototype form.
These were an inch smaller in diameter than the production
units.
In 1997 after realizing that the future belonged to the sport
compact market Mr. Paul designed an even smaller unit. No longer
having the facilities to build superchargers Richard sought out
someone who could manufacture some prototype parts. This lead to
the introduction of Dana Cox to the formula. The first work done
by the two was actually a full size 1800 CFM unit from billet
for a 600 cu in aircraft engine. From this experiment came some
fresh ideas for the manufacturing presses.
This idea was married to the newest compact design and the
current blower was the result. This unit now uses four of five
stages and an internal planetary gear set. Weighs in at about
12lbs, is 5 in diameter and about 10 inches long.
Thus came
Axialflow
Engineering Co.
The first application was directed at the new Mazda RX-8. This
is proving to be a big development project but a drivable
prototype is expected shortly. The interaction with Mazda owners
and tuners led to the interest in the car itself and the
production of other components was by popular demand.
Currently the
Short Shifter for RX 8's is available.
Under development for the future are several products, among
them Four way strut brace for the front and a rear brace as
well. Additionally is a master brake brace and center body tie
brace.
Our interest in developing this car will continue to produce new
ideas and product.
|
|